Understanding the intricate world of 12 needle embroidery machine service is crucial for enthusiasts and business owners alike. These machines, lauded for their capability to produce vibrant and complex designs, stand as pinnacles of innovation in textile manufacturing. To maintain their efficiency, a deep dive into service and maintenance becomes necessary, ensuring the longevity of the machine and the quality of its output.
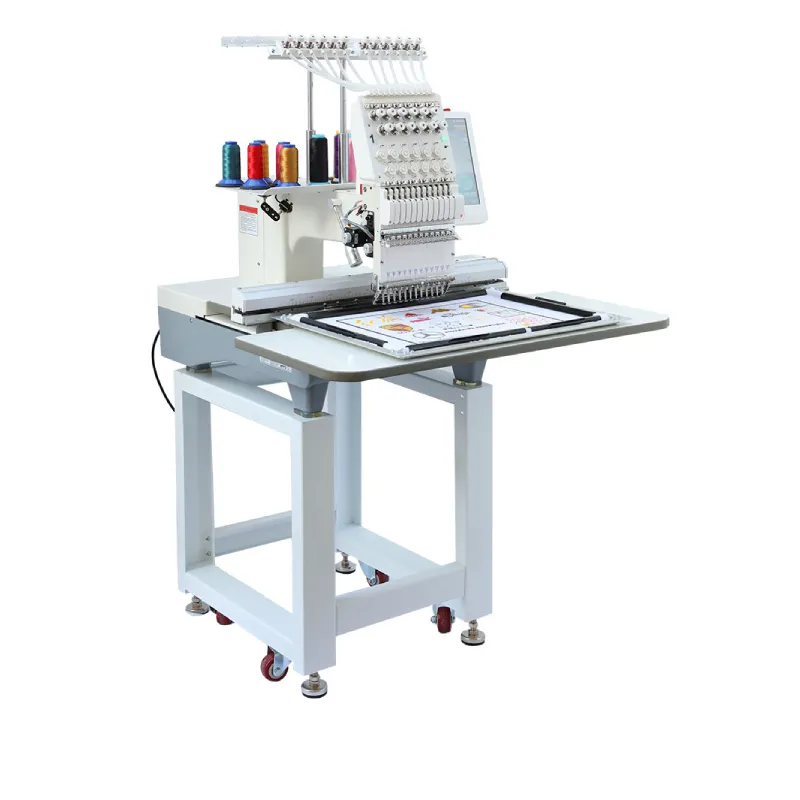
Having worked extensively with these machines, experts understand the nuanced mechanics that demand regular service. A 12 needle embroidery machine integrates both sophisticated technology and mechanical components, making it imperative for operators to have, or to employ, significant technical expertise. The first step to ensuring optimal performance is familiarizing oneself with the machine's manual. Many manufacturers provide detailed guidelines that include maintenance schedules, troubleshooting tips, and parts replacement diagrams that offer a foundational level of understanding about the intricate systems at play.
From experience, the operational efficacy of these machines can be fundamentally preserved through consistent preventive maintenance. Regular cleaning is vital, and professionals recommend using compressed air to remove dust and thread fibers from the machine's delicate parts. Additionally, lubricating moving components with manufacturer-recommended oils can vastly reduce wear and tear.
These simple actions prevent service interruptions and enhance machine longevity.
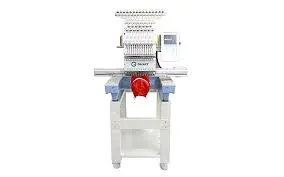
Expertise in performing these tasks confidently stems from comprehensive training sessions, often provided by manufacturers. These sessions are designed to familiarize the operators with the machine's inner workings, covering aspects from threading techniques to tension adjustment specific to the 12 needle setup. Mastery of the tension mechanism is particularly crucial, as improper tension can result in unsatisfactory stitch quality—an issue that can offset productivity and affect client satisfaction.
Authoritativeness in the field of embroidery machine servicing is not solely bestowed upon the expertise of operators but is also linked to the credentials and experience of the service technicians. Professional technicians possess in-depth knowledge backed by certifications from the machine manufacturers. They can diagnose deeper issues, such as software malfunctions or mechanical failures, that a typical user might not be equipped to handle. Establishing a relationship with a certified technician can provide a safety net, ensuring that when significant issues arise, they can be addressed swiftly and efficiently.
12 needle embroidery machine service
Trustworthiness, as measured by customer satisfaction and machine reliability, is earned through consistent and meticulous adherence to service protocols. Users report that machines with a well-documented service history tend to perform more reliably. Logging every maintenance procedure, including dated records of oiling, part replacements, and any unusual incidents, creates a valuable reference for I future servicing needs and potential resale.
Achieving a holistic approach to service also encompasses software updates. Advanced embroidery machines operate with complex programming that requires regular updates to introduce new stitching patterns, more efficient algorithms, and enhanced user interfaces. These updates not only expand the functional capabilities of the machine but also fortify security measures against potential cyber vulnerabilities.
Investing in quality parts is equally important. When replacements are necessary, always source components directly from the original manufacturer or certified distributors. This guarantees the parts will have the perfect fit and function as intended—a critical factor in maintaining machine precision.
Extending beyond mechanical service lies the nurturing of operational knowledge. Platforms such as online communities and forums where embroidery professionals congregate offer a wealth of information and shared experiences. Engaging with these platforms allows operators to exchange tips, share troubleshooting insights, and stay abreast of the latest industry advancements.
To conclude, the effective service of a 12 needle embroidery machine is a multilayered endeavor combining preventive maintenance, expert knowledge, professional servicing, and community engagement. By adhering to these practices, operators can expect not only to preserve the machine's operational integrity but also to produce consistently high-quality embroidery that meets or exceeds the anticipated aesthetic standards. This diligently maintained machine, supported by a network of experts and peers, becomes a reliable partner in textile creativity and business success, embodying the best of Experience, Expertise, Authoritativeness, and Trustworthiness.