The world of computer embroidery machines has undergone a dramatic transformation in recent years, setting new standards for efficiency and creativity. This evolution has made servicing these machines vitally important for businesses and hobbyists alike. Providing comprehensive service for computer embroidery machines enhances their performance, ensures longevity, and boosts productivity, thus making it a focal point for companies that want to maintain a competitive edge.
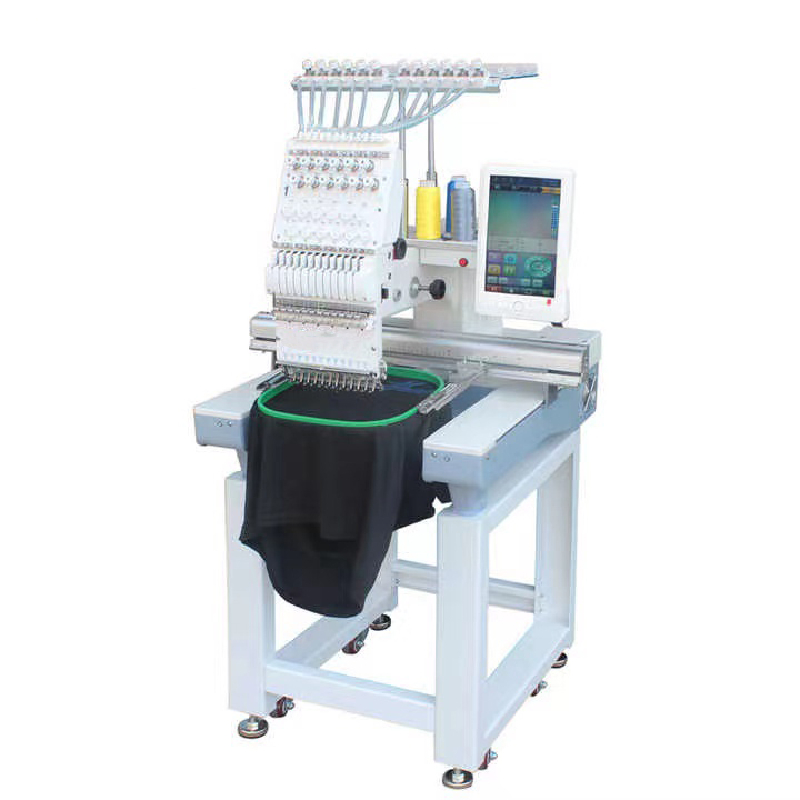
Computer embroidery machines are remarkably complex, embodying sophisticated technology that requires proper maintenance and service. Overlooking the service aspect can lead to increased downtime, which directly impacts a business's bottom line. Expertise in servicing these machines not only ensures operational efficiency but also maximizes ROI by prolonging machine lifespan. This requires technicians with a deep understanding of the mechanics and electronics that drive these machines, an essential area of expertise that can only be developed through rigorous training and extensive practical experience.
Comprehensive service begins with a diagnostic evaluation, identifying existing issues and potential future problems. Expertise in this initial step guarantees that issues are caught early, safeguarding the machine against long-term damage. High-quality service should incorporate both hardware adjustments and software updates. Maintenance of the mechanical components, like needles, thread guides, and loopers, prevents wear and tear, while the latest software updates enhance functionality and integrate new features.
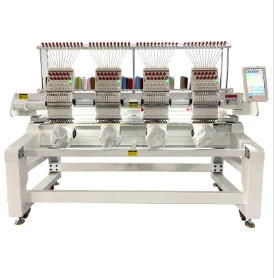
Professional service also involves calibration of the tension, ensuring that it is set correctly to produce uniform stitches. Incorrect tension settings can result in poor stitch quality, potentially damaging fabrics and affecting the final product. An authoritative service provider possesses the knowledge to perform precise tension adjustments, guaranteeing optimal stitch quality at all times.
A critical aspect of authoritative machine service is the use of genuine replacement parts. Some providers might opt for cheaper, non-OEM parts, which can compromise machine performance and void manufacturer warranties. Trustworthy service providers rely on OEM parts to maintain the machine’s original specifications, thereby ensuring its continued reliability.
computer embroidery machines service
The dependability of a service provider can be measured by their commitment to customer education. Sharing insights and best practices for machine care empowers users, enabling them to perform routine checks and basic troubleshooting. This proactive approach reflects a service provider’s expertise and authority, as they prioritize the long-term satisfaction and success of their clients.
Emphasizing regular service routines is a cornerstone of maintaining trust. Predictive maintenance can help anticipate issues before they transform into costly repairs. This practice not only minimizes machine downtime but also strengthens the service provider-client relationship, as clients learn to rely on consistent, preventive care, which speaks to the provider’s expertise and reliability.
Innovative service practices may include remote diagnostics and online support, which are indispensable in the age of connectivity. Service providers who offer these advanced options are better positioned to address issues swiftly, thereby enhancing trustworthiness through real-time solutions and support.
Ultimately, the key to exceptional service lies in the fusion of experience, expertise, authority, and trustworthiness. Clients need more than a quick fix; they require a service partner dedicated to optimizing their machinery for peak performance. Recognizing the intricacies involved and consistently delivering high-quality, comprehensive service ensures that computer embroidery machines continue to operate smoothly, allowing businesses and hobbyists to focus on creativity and productivity without the worry of machine failure.