A six-head embroidery machine is a transformative asset for businesses in the garment and textile industry. These machines are complex, high-performance equipment designed to boost productivity by simultaneously working on multiple pieces, which is crucial for meeting bulk embroidery needs. Ensuring they function optimally requires a dedicated focus on maintenance and service.
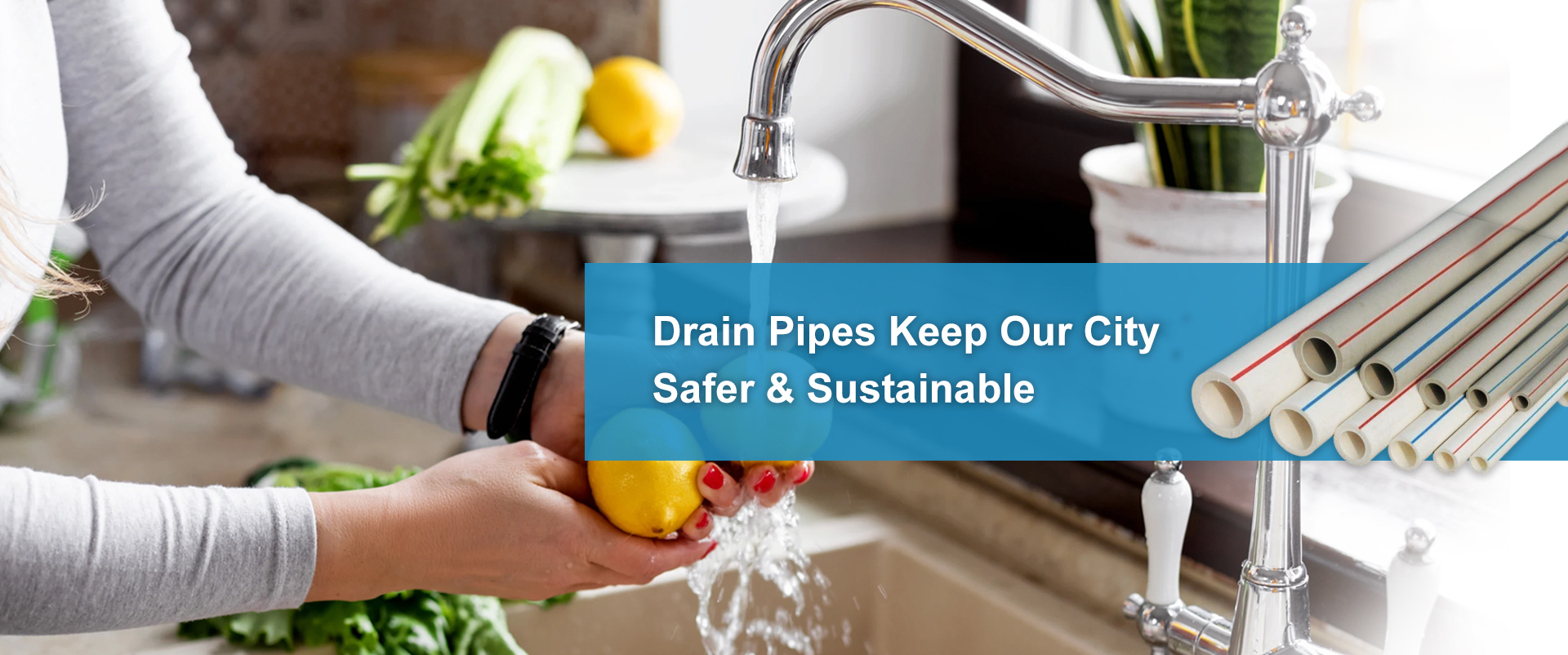
The experience of managing a six-head embroidery machine begins with understanding its intricate parts. Each head of the machine is equipped with needles, threads, and bobbin cases that are synchronized to create intricate designs with precision. Timely and professional servicing of these components is vital to ensuring seamless operation. A malfunctioning head can disrupt the entire process, leading to costly delays and inconsistencies in production.
Expertise in maintaining and servicing these machines involves more than routine cleaning and oiling. While these are fundamental tasks, a service strategy must also include regular checks of the machine's tension settings, alignment, and software updates. Tension settings are crucial as incorrect tension can lead to poor-quality stitching or even damage the fabric. Technicians with expertise in embroidery machines should possess a deep understanding of the different fabric types and the necessary adjustments to accommodate them. Similarly, software regular updates are essential in modern machines, enabling them to handle complex designs with improved efficiency.
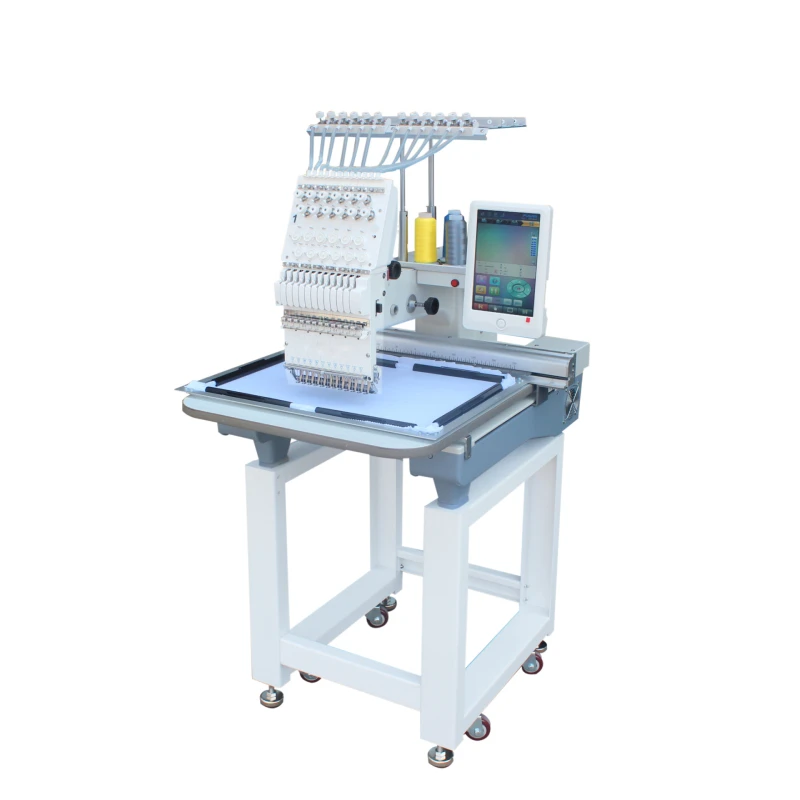
Authoritativeness in this field is marked by the ability to troubleshoot and resolve unexpected issues quickly. Machines can encounter varied problems such as thread breaks, needle breaks, or misalignments. Being authoritative means having the knowledge to immediately identify and address these issues, minimizing downtime. Companies that specialize in the servicing of six-head embroidery machines often provide training sessions for in-house staff, which is invaluable. This not only ensures that staff are able to perform minor repairs independently but also enhances their understanding of the machine’s operational nuances, thus contributing to improved productivity.
embroidery machine 6 head service
Trustworthiness is built through consistent, high-quality service and support. Establishing a partnership with a reliable service provider assures continuous optimal performance of the embroidery machine. Regular visits from a certified technician can prevent larger, more costly breakdowns and extend the lifespan of the machine. It also instills confidence in the production schedule, knowing that the equipment will reliably perform at capacity.
Moreover, a trustworthy service provider often offers a warranty and fast response times in emergencies, reducing operational disruptions. Transparency in the service process, with detailed reports on each service, helps in forecasting future service needs and budgeting for repairs. Trustworthiness also extends to using genuine parts during repairs, which are designed to fit and function seamlessly with the specific make and model of the machine, avoiding potential misfit issues and warranty voids.
In conclusion, effectively managing a six-head embroidery machine requires a comprehensive understanding and approach to its service and maintenance. The experience gained through consistent practice, the expertise developed through specialized training, the authoritativeness to act swiftly in resolving issues, and the trustworthiness built through reliable service are all integral to keeping these machines running efficiently. These factors not only ensure longer machine life and better embroidery quality but also significantly contribute to the business’s ability to meet production demands efficiently. In the competitive world of embroidery, maintaining your equipment is not just about keeping it running; it’s about elevating your production capabilities and securing your business’s reputation for quality and reliability.