Navigating the world of custom embroidery can be daunting, especially when it comes to choosing the right equipment and ensuring its optimal performance. Single embroidery machines, praised for their versatility and precision, are often the go-to equipment for businesses ranging from small boutiques to large-scale textile companies. However, maintaining these machines requires a dedicated service approach that underscores experience, expertise, authoritativeness, and trustworthiness—key pillars that ensure longevity and efficiency.
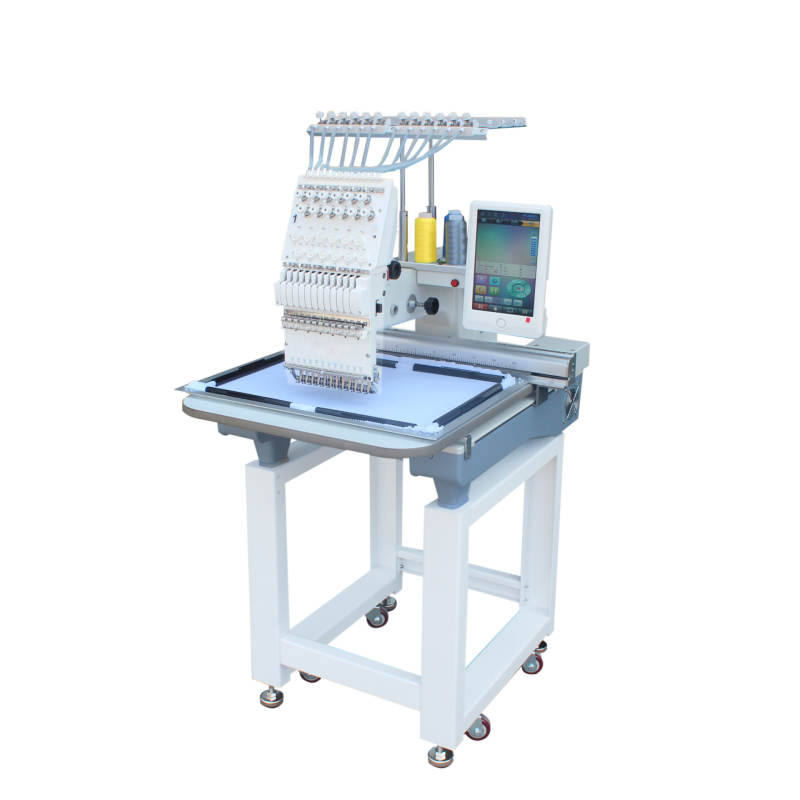
To fully appreciate the role of single embroidery machine service, it's essential to explore the practical experiences of experts who have spent years refining their craft. A seasoned embroidery technician emphasizes that routine maintenance is the cornerstone of smooth operations. Regular checks and calibrations prevent minor glitches from escalating into more severe issues that can halt production lines unexpectedly. By establishing a proactive maintenance schedule, operators preserve the machine's accuracy, ensuring consistent stitching quality and reducing downtime—a critical component in meeting tight deadlines and maintaining customer satisfaction.
Expertise in servicing single embroidery machines goes beyond routine maintenance. It involves a deep understanding of the machine's mechanics, software intricacies, and the unique demands of diverse fabrics. Crafting intricate designs on delicate materials requires precise needle settings and thread tensions, adjustments that only a knowledgeable technician can accurately perform. This expertise ensures that the machine functions at peak efficiency, minimizing waste and maximizing output—a crucial factor for businesses aiming to scale their operations and enhance profitability.
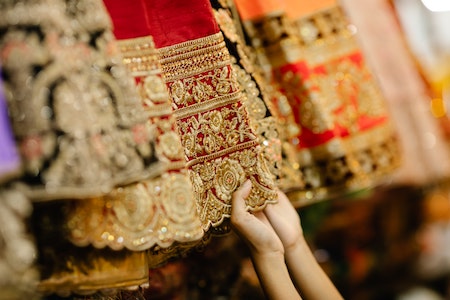
Authoritativeness in the field of single embroidery machine service is established over years of proven reliability and innovation. Leading service providers often attend international textile and technology conferences, staying abreast of the latest developments in embroidery technology. By doing so, they not only enhance their technical skills but also contribute to the industry by integrating cutting-edge techniques and machinery advancements. Such authority is reflected in client trust, as businesses seek out these well-regarded experts to handle their embroidery needs, knowing they will receive service characterized by precision and reliability.
single embroidery machine service
Trustworthiness in machine servicing is crucial, given that these machines represent a significant investment for any business. Transparent service contracts, upfront cost estimates, and clear communication about potential challenges foster a robust relationship between service providers and clients. Trust is further reinforced by a track record of timely service delivery and successful machine restorations, reducing business disruptions and safeguarding the firm’s reputation. Machine servicing companies that prioritize these values often enjoy long-term partnerships with their clients, a testament to their dependable service and commitment to quality.
A comprehensive single embroidery machine service also involves training operators to handle minor maintenance tasks and troubleshoot common issues. Service providers frequently offer bespoke training sessions, equipping operators with the skills necessary to maintain their machines effectively. This empowerment ensures that businesses have the internal capability to manage urgent situations, reinforcing the safety net that full-service support structures provide.
In conclusion, single embroidery machine service is an intricate dance between technical acumen, proactive maintenance, continuous learning, and building trust. When executed with precision, it enables businesses to operate smoothly, innovate boldly, and compete vigorously in the bustling world of customized apparel and textiles. Whether for a burgeoning start-up or an established enterprise, effective machine maintenance is not just a service—it's a strategic asset.